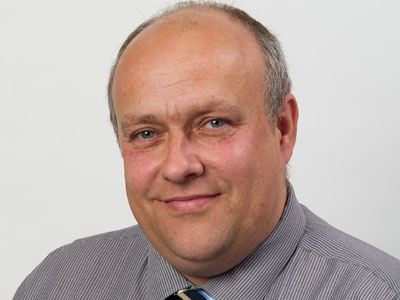
Author: Darren Bryant, Area Sales Manager, Condair Limited
Automotive paintshop humidification
By maintaining the correct humidity in sand decks and paint spray booths productivity through these areas can be increased by as much as 10%, with more cars being passed first time after inspection.
Sanding Decks and Inspection Stations
The main objectives in humidifying a sand deck are to suppress dust and reduce the static attraction of the paint dust and other foreign bodies to the bodywork. By maintaining an optimum humidity of 55%rh (relative humidity), the moisture content of the air changes the electrical charge of the dust so that it is the same as the surface of the car. This results in the dust running off the bodywork of the car instead of holding to it.
As a result, dust from the air and the sanding process is more easily removed from the surface, providing a cleaner shell for repainting or the following paint application. This reduces production time, reduces blemishes and improves the quality of the finish. It also means that more cars pass through inspection first time, as there are fewer imperfections and sanding isn’t required.
The type of humidifier typically used in these applications is a direct air spray humidifier, like the JetSpray. Cold water from the plant’s demineralised supply is first purified via a UV sterlisation system before being combined with compressed air in a precision engineered nozzle. The nozzle releases a very fine spray of moisture into the atmosphere, where it instantly evaporates raising the humidity to the required level.
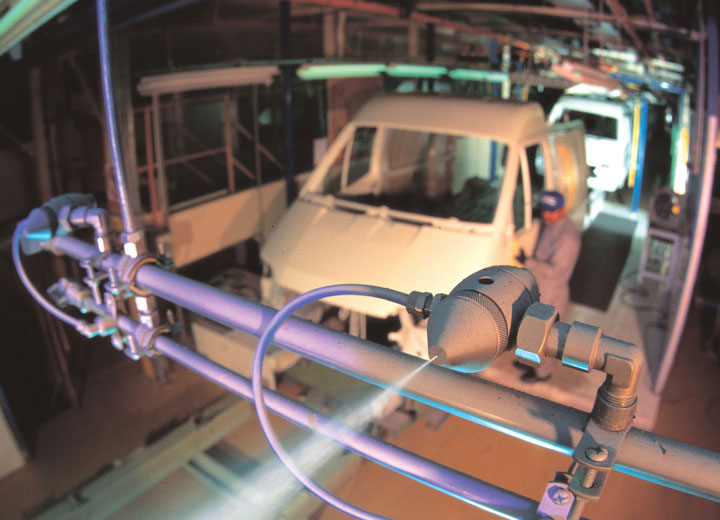
The type of humidifier typically used in these applications is a direct air spray...
For this type of application it is important that a demineralised water supply is used for such nozzle-based systems. Whilst humidifiers are often designed to cope with the mineral content of the water, with features like self-cleaning nozzles that prevent blockage, the mineral dust that remains in the air after the sprays have evaporated will simply add to the problem.
The specification of a nozzle-based humidifier must also include a guarantee that the equipment is silicon-free. Water-based paints, in particular, are very sensitive to even a minute amount of silicon in the air when the element settles on the surface to be painted. The lacunae or small craters that result during painting are difficult to remove and will continue to affect future paint applications.
There are three basic ways to add moisture to the air in order to raise the relative humidity: introduce steam into the air, introduce cold water as droplets into the air, or pass dry air through a moist surface to raise the relative humidity through evaporation. So, what makes a cold water, direct air spray more appropriate than the other two for this application?
Sand decks and paint inspection areas are typically situated at the delivery end of the conveyorised ovens that bake the paint coat onto the surface of the vehicle body. These well-insulated ovens typically lack a cooling facility meaning that the metal bodies destined for inspection and preparation are hot. These hot body shells mean that the temperature on the deck is often high and, combined with the warm air escaping from the oven and heat from the bright illumination required in these areas, create an environment that can be as hot as 40oC. This is uncomfortably high for the workforce and so ventilation systems are used to reduce this temperature to more acceptable, productive levels.
However, ventilation is commonly ineffective. The sheer volume of the air required to displace the hot air is so high that it drives the cost of the air handling systems to disproportionate levels. Without careful design of low velocity delivery systems, the air movement itself becomes uncomfortable and also blows dust around. Even in a well-designed ventilated area served by a humidified air conditioning system, it’s impossible for the relative humidity to be maintained above the effective antistatic threshold of 50%rh. For example, a ventilation system delivering very cold air at 10°C with a high relative humidity of 90%rh, which succeeded in achieving a working condition of 30°C, will only provide 25%rh due to the humidity of the air decreasing as its temperature rises.
It is therefore most appropriate to raise the humidity directly where it’s needed, on the deck. Technically, evaporative systems cannot deliver sufficient moisture without creating excess air movement, leaving spray nozzles and steam. The benefits using direct air spray system are that energy costs are less than a tenth of those required to run a steam system, the maintenance needed is low compared to steam and, as the spray evaporates, there’s an adiabatic cooling effect that drops the temperature by several degrees, which isn’t available from steam. This “free” cooling is very welcomed by staff.
A system like the JetSpray, with a long history of successful use in the automotive industry, is ideal. Designed to produce fine sprays without the risk of droplets or drips, they are installed close to the work stations at low level, and prove effective in maintaining a more comfortable, productive environment. Some long sand decks may have in excess of 1,000 nozzles feeding thousands of litres of moisture each hour into the atmosphere.
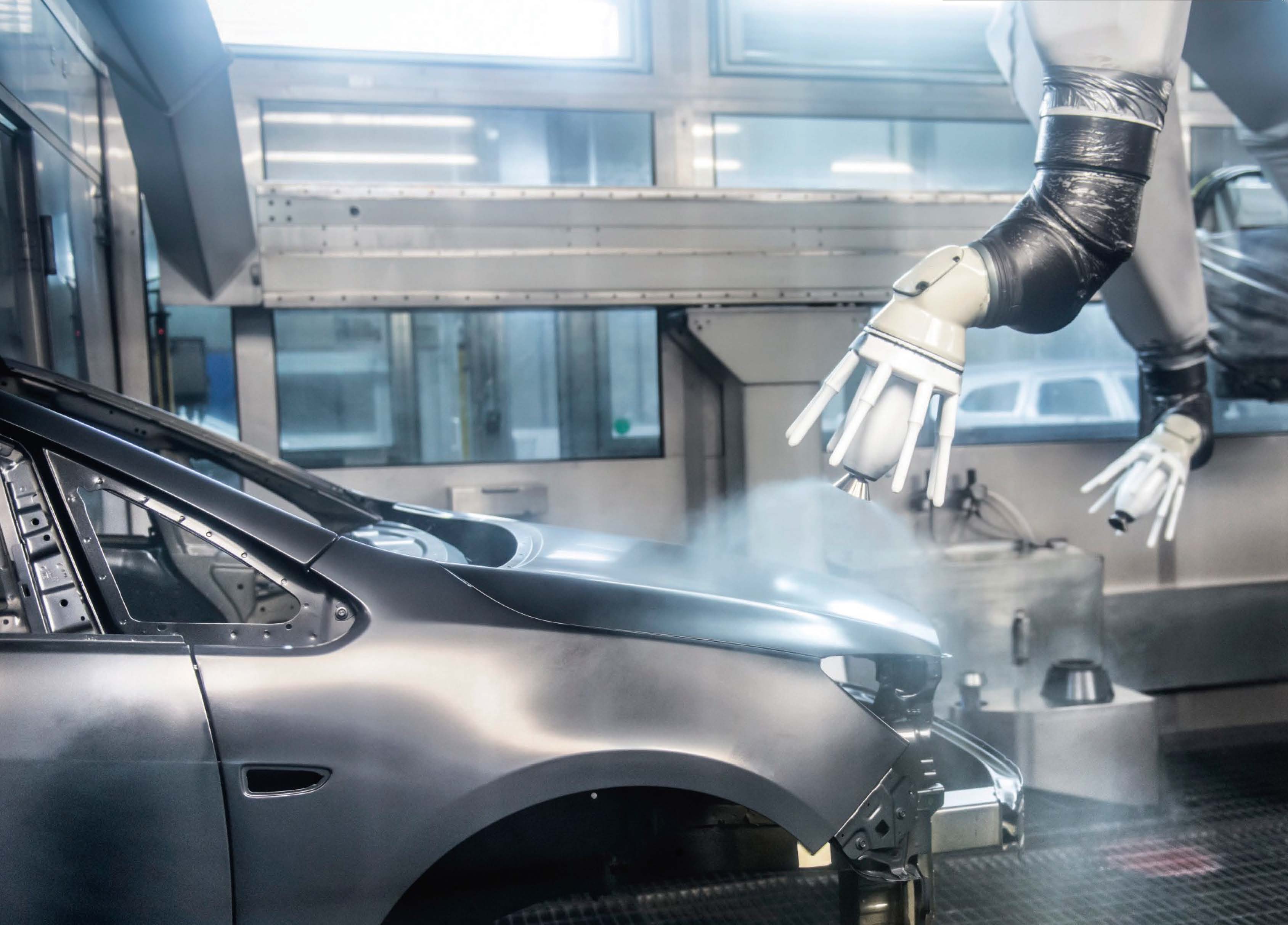
The objective of humidifying a paint spray booth is to permit the optimum transfer of paint...
Paint Spray Booths and Spray Areas
The objective of humidifying a paint spray booth is to permit the optimum transfer of paint from the spray guns to the bodywork, without any loss into the atmosphere of the water-based paint itself.
This has two benefits. Firstly, a cost benefit of not “losing” paint to evaporation and more importantly, of transferring the paint to the bodywork surface in its original state for maximum quality of finish and fewer imperfections, thereby saving costs by reducing post-paint sanding.
The optimum humidity for this transfer is 72%rh, although this might vary according to the paint supplier concerned. At this level of relative humidity, the paint is in equilibrium with the atmosphere, keeping losses to a minimum. If this humidity is not maintained, the bodywork will need more attention in the sand deck after spraying. One major manufacturer, humidified by Condair, was able to increase its percentage of first time passes through post spray booth inspection by 10% through improving the humidity control in the spraying area.
As the air is fed to the spray booths via ductwork, fed by large air handling units, the humidifier used for this application is located in the air handling unit or duct itself. It humidifies the air which is then fed into the booths. Historically, the type of humidifier used for this application was a spray washer system. This sprays water directly into the air flow and, with evaporation of the droplets, raises the relative humidity to the desired level. Unevaporated droplets are recovered by a system of vanes or on a refrigeration coil, collected in a sump and recirculated for use again.
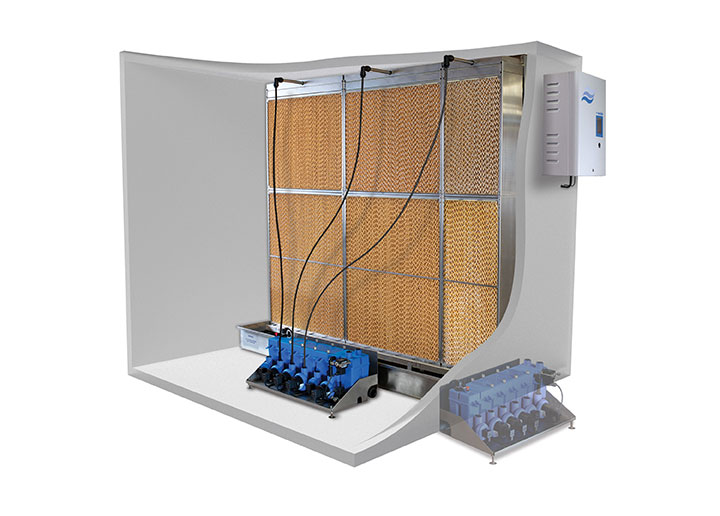
The Condair ME is easy to install inside the duct and has very low running costs....
However, these systems are very inefficient as they only atomise about 10-15% of the moisture they release, resulting in very wet duct sections and water damage to ductwork and an increase in maintenance requirements. Most of these humidifiers were also installed with little or no hygiene features such as UV sterilisation or anti-microbial filtering, which can potentially lead to staff suffering what has been called “humidifier fever” - flu-like symptoms such as a tight chest, headaches and sore eyes. There’s also a risk of Legionnaires’ disease if infected droplets are carried downstream and inhaled by workers.
Nowadays these old spray washer humidifiers are being replaced with much more efficient and hygienic evaporative humidifiers, like the Condair ME. These systems fit inside the air handling unit, in the same sort of situation as a washer system might be installed. They pass water down over a high surface area matrix through which the air flows. The air picks up moisture as it flows through the wetted matrix and becomes humidified, without any droplet carry-over.
The Condair ME is easy to install inside the duct and has very low running costs – 13 times less than atomising spray humidifiers. The high levels of humidification required typically make the running costs of steam too great to consider. Advanced safety and hygiene features ensure that all water in the system is clean and if the system is not operating, the water will drain out of the unit, so there’s no risk of stagnation, for added peace of mind.
Choosing the Right Humidifier
Given the enormous benefits of humidification to the industry, it’s no surprise to discover that most large manufacturers use humidifiers within the painting and finishing process, particularly since the wholesale move to water-based materials.
However, what is surprising is that even leading and globally recognised manufacturers with modern plant have been wrongly advised and left with humidification systems that either fail to deliver the required levels of humidity at all, or operate inconsistently. Production problems caused by low or fluctuating relative humidity aren’t always easy to identify as the moisture content of the air isn’t readily tangible compared with more obvious factors such as temperature. A recent, high-profile example with a brand new, custom-designed facility was equipped with inadequate steam humidifiers that not only failed to deliver the right relative humidity but also suffered very high running costs and ate into the HVAC maintenance budget in a significant way.
It is important to ensure that your chosen supplier not only offers a range of humidifiers, and so has a choice, but also has the experience and understanding of the processes concerned to ensure that what is delivered is appropriate. Even though cold water systems might be right for paint spray and inspection areas, the very close control afforded by some types of steam humidifier, such as the Condair MK5, often makes it the right choice in engine testing areas, particularly where the demands are highly specific such as in Formula 1 engine tuning.
Looking after your Humidifiers
Industrial health and safety is, quite rightly, far more stringent than ever before and humidifiers are no exception to this. Specific legislation exists regarding humidifiers and, whichever humidifier is used, it is important to consider it as part of the water system in the plant as a whole. Health and Safety Executive guidelines in the UK concerning Legionnaires’ disease makes it an obligation to include all humidifiers in the risk assessment for a building and to have a monitoring and control scheme in place, which is documented.
Mechanically, it might seem that a device which either sprays, boils or evaporates water is a simple machine that can be ignored and left to operate unattended. Modern cold water systems are far less labour intensive than steam and have far fewer serviceable items to replace. With features like fail-safe UV sterilisation and purge systems, they’re also a lower risk to health than older cold water systems. However, all humidifiers need regular inspection and maintenance to keep them running efficiently and this should form part of your planned maintenance schedule. It’s worth ensuring that maintenance staff are appropriately trained by your supplier so they understand the equipment and know what’s required.
It’s also important to be sure that your supplier has a proven record of effective support and that they’ll still be in business when you need them. For efficient production in the paintshop, you can’t afford to be without your humidifier!